Search the Internet for “fiber optic connector inspection” and you will certainly see a lot of infor mation from just about every company you – associate with fiber optic communications. Everyone in the fiber installation and network world is talking about inspection. In a study by NTT-Advanced Technology, 98% of installers and 80% of network owners reported that issues with connector contamination were the greatest cause of network failures.
As bandwidth demands rise and loss budgets get tighter, specks of dust and dirt, oils, and anything else on a connector end face can wreak havoc on network performance. In the world of fiber optics, where light is transmitting through an 8-micron fiber core, a speck of dirt can be likened to a boulder in the middle of the road. It does not take much to put that low loss connector out of commission.
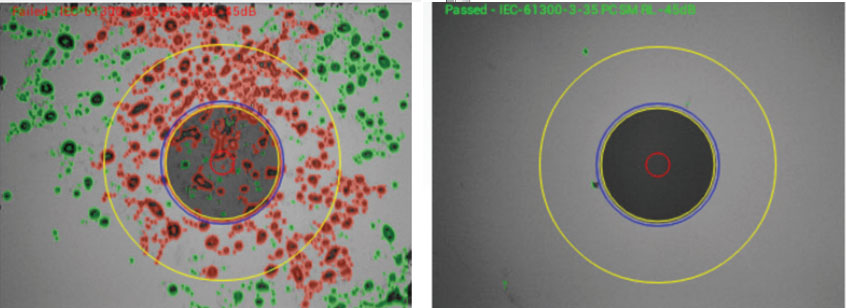
The push for tighter specs has prompted a wide variety of connector inspection solutions both for manufacturing facilities and for the field. Unfortunately, many of us have realized that connector dust caps are just that: caps with dust in them. Even a very carefully controlled manufacturing environment does not ensure that your connectors are ready for mating when they arrive on site.
With so much riding on your network, cleaning and inspecting are worthwhile pursuits that can prevent the need for costly troubleshooting and truck rolls later.
Seeing Is Believing
Many types of inspection tools are available for field use today. Most manufacturers of test equipment offer standalone field scopes for viewing connector end faces. Many also provide scopes that plug into an OTDR or another platform with a display that will show the connector on the screen. A new option provides a Wi-Fi connection to your phone or tablet with a free app. There are software tools that compare the connector before and after cleaning and software upgrades that provide automatic pass/fail analysis against
pre-set industry or customized standards. (See Figure 1.)
Every vendor will give you a reason to buy its solution, but in the end, all would agree — get something to inspect your connectors. Make inspection and cleaning part of your installation/test standard practices and reap the rewards in the long run.
In order to properly evaluate a connector, the end face is sectioned into different zones radiating outward from the center of the core of the fiber. Standards have been set by IEC 61300-3-35 that define the characteristics of any dirt, dust, or scratches that can be found in a specific zone. Criteria are specific to MM and SM, UPC and APC and ribbon fiber connectors. The strictest requirements are, of course, found in zone A — the core of the fiber. (See Figure 2.) .
For anyone who has wiped a connector on is/her sleeve or the palm of his hand or used a regular tissue: please stop! Special materials, wipes, and tools for cleaning fiber connectors have evolved over the years for a reason. They must remove anything on the connector and leave nothing else behind. (See Figure 3.)
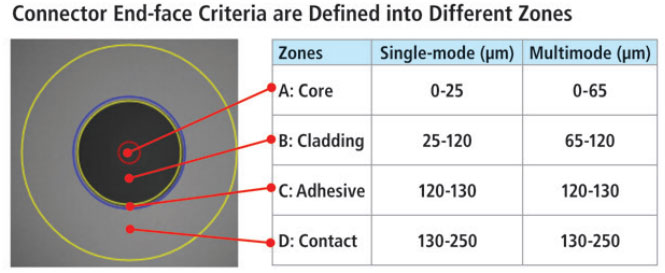
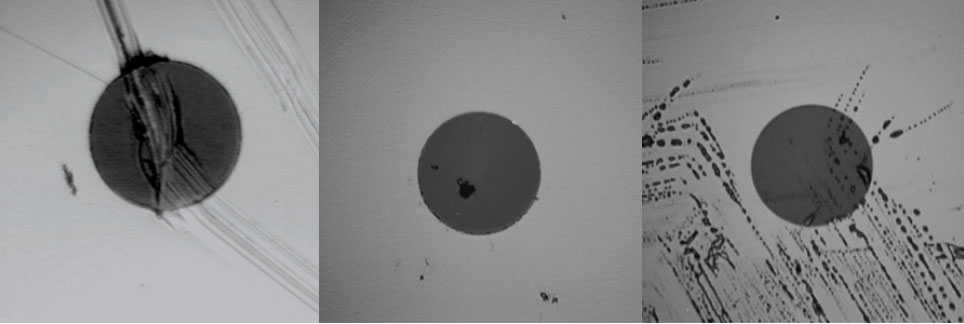
Even the right products sometime need a second swipe to get everything clean. By inspecting before connecting, you can be sure that all is clean. Some dirt and oils require more than a dry cleaning solution to really get clean. But, be cautious of wet cleaning, as this can also leave a residue.
Once a connector has been properly cleaned, an inspection scope can provide only a visual check that will be subjective and relies on the technician to determine if this is “clean enough”. Automated products that include pass/fail analysis will provide results based on accepted industry standards, and better ensure clean mating and optimum performance. These products have software designed to quickly measure all defects found in the field of view, evaluate the size of the defect against the standard being used for each zone and then reporting if the end face is within specification or not. Whichever option you choose, most vendors will agree that good practice is to inspect all fiber connectors before mating.