Making the Right Fiber Cable Choice can Improve Overall Performance of Distribution Cables in the PON
In the distribution portion of the passive optical network (PON) for fiber-tothe-premise (FTTP) architectures, the choice of fiber cabling – ribbon vs. loose tube – can directly impact ease of installation and future performance. As is usually the case in these networks, specific architectural characteristics and particular applications may dictate the deployment of one type of cable over the other. However, ADC’s experience in developing and manufacturing FTTP network equipment has concluded that in most cases, ribbon cable provides a considerable performance advantage over loose tube in the distribution portion of the PON network.
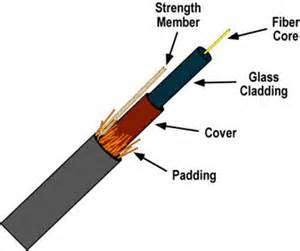
Fiber Density is Key
The most obvious asset for ribbon cable is its higher fiber density. This is particularly important for upstream applications requiring high fiber-count cables. Material costs decrease since less plastic is involved and fewer strength members are required. Additionally, it takes significantly less termination time (and cost) with ribbon cable because of its mass fusion splicing capability as compared to one-by-one fiber splicing. Even with techniques available for “ribbonizing” loose tube fibers – basically stacking the fibers and using a spray adhesive to simulate ribbon cable – for mass fusion splicing, using ribbon cable to begin with eliminates the need for this extra step.
Ribbon is, therefore, a better choice for termination in areas of the network that require a high volume of fibers. As the network branches farther out towards the premise, the need for high fiber-count cables decreases. Once the density becomes less than 144 fibers, loose tube cables have certain advantages. For example, loose tube cables offer the ability to peel off single tubes to access up to 12 fibers without disturbing the other fibers within the cable – even when information is being transmitted through the rest of the cable. Although this is possible with ribbon cable, it is a much more difficult operation since by accessing one particular fiber, all the ribbons are exposed to activity that could result in problems and even outages.
Hybrid Designs
Hybrid ribbon and loose tube designs exist for some applications. For these applications, ribbon stacks are put into loose tubes and the tubes are stranded together. Although this provides the ability to access individual ribbons, dealing with the ribbon stack is still less desirable. These cables tend to be much larger and involve more plastic. Thus, much of the density advantage is lost. They are also more expensive, and the only advantage would be to gain higher fiber counts than could be achieved using a central tube design.
Typically, cable vendors like Sumitomo Electric Lightwave, offer ribbon cables that contain 864 fibers as compared to 288 fibers in loose tube configurations. Although higher density loose tube cables are possible, they require more plastic – making them prone to attenuation problems caused by expansion and contraction of the plastic with varying temperatures. This leads to the need for more strength members coupled to the elements to ensure minimal shrinkage.
Connectorized Distribution Requires Ribbon Cable
Large loose tube cables are much more thermally challenged than dense ribbon cables, making them less ideal for the outside plant of the PON. However, even the ribbon cable in the fiber distribution hub must perform as intended over the temperature ranges. It’s been ADC’s experience that for connectorized distribution cabling inside the FDH, putting connectors on ribbon cable works far better than any loose tube cable because of the thermal expansion and contraction of the sub-units.
In temperatures starting at about 2 degrees F, the tubing in loose tube cables contracts substantially while the fibers remain in place. This phenomenon induces cable loss caused by attenuation in connectorized loose tube distribution cables of as high as 10 dB. There are only two ways to accommodate the expansion and contraction of the sub-units. One way is to slit the sub-unit material to make it “free-floating” over the fibers. This isn’t recommended since it leaves multiple fibers unprotected. The second alternative is simpler – choose a vendor whose products exhibit less of this
phenomenon or who has achieved a time-tested way to mitigate it. Most manufacturers of loose tube cable recommend maximum tube lengths of 8 feet outside of the OSP jacketing. Even at these lengths, TE has often observed considerable shrinkage of buffer tubes, leading to temperature-induced losses at high wavelengths if the cable assembly is not properly designed.
Ribbon cables simply do not have this problem. It’s avoided by having all the cables in a central tube that allows ample room for the fibers to move around as sub-unit materials expand and contract. Although it may not be considered a significant advantage, ribbon cables eliminate the need for additional strength members to prevent the end affects of temperature-induced cable loss. However, it is one less operational step required and ultimately saves additional space.
All Things Considered
Connectors are often advantagous at any location that may require access for strategic testing or incremental growth. While TE never advocates replacing splices with connectors when it doesn’t absolutely make sense, using connectorized ribbon cables for distribution within the PON of the FTTP system definitely makes sense. In terms of restoration following a major event such as a cut cable, it is much easier to restore a ribbon cable versus a loose tube cable.
Since capital expense must inevitably be addressed at some point when deploying an FTTP network, it may be important to make a comparison between the relative costs of ribbon versus loose tube cable. According to Sumitomo Electric Lightwave, the cost of ribbon cable is generally higher for fiber counts of 72 or less. For counts above 72, the cost differential is less pronounced and diminishes further as fiber counts increase.
There is no real cross-over point whereby ribbon cable is less expensive then loose tube cable. However, most customers are selecting ribbon cable on the basis of its productivity, size, and other benefits that far outweigh the initial cost differential.
All things considered, TE has concluded that in feeder cables where lower fiber counts are required, loose tube cables are sometimes a good choice based on first cost. However, on the distribution side of the FDH, a connectorized ribbon cable simply performs far better than a connectorized loose tube cable. When giving careful consideration to issues such as size, density, and restoration of cables, it appears ribbon cables are the best choice.